Die Eisenhütte Engelsberg (Engelsberg
bruk) in Ängelsberg bei Fagersta in der Region Bergslagen ist
eine gut erhaltene Eisenhütte mit Gebäuden und intakten Industrieanlagen aus dem
18. und 19. Jahrhundert. Dieser Typ von Eisenhütten machte Schweden zu einem
weltweit führenden Hersteller von Eisen. Die Eisenhütte Engelsberg erhielt ihren
Namen von dem Bergmann Englika, der hier die erste Gießerei errichtete. Der
Hochofen in
Mulltimmerbauweise ist einer der wenigen noch erhaltenen in Schweden. Die ältesten Teile des Hochofens stammen aus
dem 18. Jahrhunderts. Die Hütte wurde 1919 stillgelegt. Engelsberg wurde im Jahr 1993 in die
Welterbeliste aufgenommen. Begründung des Welterbekomitees: Die Eisenhütte
Engelsberg ist ein einmaliges Beispiel für eine Industrieanlage aus der Zeit des
17.-19. Jahrhunderts mit wichtigen technischen Überlieferungen sowie intakten
Administrationsgebäuden und Wohnhäusern. Die schwedische Eisengewinnung mit Hochöfen begann im 14.
Jahrhundert. Im 17. Jahrhundert wurde über ein Drittel der Weltproduktion an
Eisen in Schweden produziert. Es entstanden immer neue Eisenhütten vor allem in
Bergslagen. Der Anteil an der Weltproduktion sank bis 1850 auf 3 Prozent.
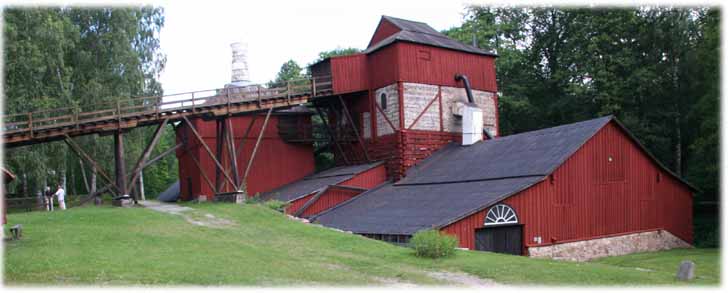
Gruben und Bergwerke
Die früheren Bergwerke wurden meist im Tagebau betrieben. Mit Feuer machte man
das begehrte Erz brüchig und brach es anschließend aus dem Berg. Man stapelte
Holzstämme gegen den Berg und zündete es an. Nach ungefähr 14 Stunden platze der
Berg von der Hitze und die Bergmänner konnten das Erz herausspitzen. Die
Abbaumethode wird in Schweden „Tillmakningsmetoden“ genannt. Als das Schwarzpulver in
den ersten Jahrzehnten des 17. Jahrhundert aufkam, wurde die Arbeit leichter.
Man sprengte Stollen in den Berg und fand immer neue Flöze im tiefen Berg. Die
Grubenarbeit wurde vorwiegend im Sommerhalbjahr durchgeführt. Nicht
metallhaltiges Gestein wurde vom Eisenerz aussortiert und auf große Halden
gefahren. Für Mineralieninteressierte sind diese Halden wahre Schatzkisten!
Immer neues Mineral wurde in Nordmarks und Långbans Grubenfelder von geschickten
Bergarbeitern und Mineralogen entdeckt. Bevor es Elektrizität gab, war es harte Arbeit, das Erz aus dem Bergwerk zu
bekommen. Im 16. Jahrhundert zogen Bergarbeiter oder Pferde mit speziellen
Winden die Kübel nach oben. Je tiefer man den Bergwerksschacht sprengte, desto
größere Probleme bekam man mit dem Grundwasser. Im 17. Jahrhundert wurden so
genannte „konstgångar“ gebaut, die ihre Kraft von einem Wasserrad an ein
Pumpwerk im Schacht abgaben. Es gab einfache und doppelt pendelnde „konstgångar“.
„Träreglor“ konnten sich mehrere Kilometer von der Kraftquelle bis zum
Bergwerk erstrecken. Sie konnten sich auch verzweigen und so ihre Kraft an Pumpen
in mehreren Schächten gleichzeitig abgeben. Für Bergarbeiter dagegen gab es keine Anordnung für den Transport zum Bergwerk.
Sie mussten über Leitern in die Gruben klettern. Die Grubenarbeit war damals mit
großen Risiken verbunden. Außer dem gefährlichen Klettern gab es ständig Gefahr
von Einbrüchen, Feuersbrünsten, gefährlichen Gasen, Gefahr bei der Sprengung
sowie kaltes und feuchtes Arbeitsklima. Viele Bergarbeiter wurden verletzt, als
Mitte des 18. Jahrhundert das leicht explosive Nitroglyzerin als Sprengmittel
angewendet wurde. Erst später verwendete man das sichere Dynamit. Die technische
und wirtschaftliche Entwicklung im 18. und 19 Jahrhundert veränderte die
Grubenarbeit. Dampfmaschinen, Petroleum und Elektrizität erleichterten den
Abbau. Aber der harte Wettbewerb auf dem Weltmarkt hatte zur Folge, dass die
mittelschwedischen Eisenerzgruben nicht länger einträglich waren. Ein Bergwerk
nach dem anderen wurde stillgelegt und 1980 wurden die letzten beiden Bergwerke
in Persberg und in Nordmark geschlossen. Die mehrere hundertjährige
Eisenerzepoche in Filipstads Bergslag war damit beendet.
Hütten
Erz, Wald und Wasserkraft waren damals Voraussetzung, um Eisen zu schmelzen. Es
war natürlich von Vorteil, wenn man die Öfen so nah wie möglich an die
Grubenfelder zu bauen, um Transportwege des schweren Erzes zu sparen. In
Hochhöfen brannte Holzkohle gemischt mit Erz und schmolz zu Roheisen. Mitte des
15. Jahrhunderts gab es die ersten Hütten bei den Stromschnellen in Filipstads
Bergslag. Diese ersten Hütten waren aus
Holz, Stein und Erde gebaut (Mulltimmerbauweise). Mit der technischen Entwicklung Mitte des 18. Jahrhunderts wurden diese „Mulltimmerhyttorna“
von Hochöfen ersetzt, die ganz aus Stein gebaut waren. In der gleichen Zeit
wurden Maschinen und Apparate entwickelt, die die Hüttenarbeit erleichterte und
verbesserte. Diese Maschinen und Umbauten der Hütten forderten Kapital. Die
Veränderungen führten zu Gesellschaften mit Anteilseignern der Hütten. Gegen
Ende des 18. Jahrhunderts waren alle Hütten zu Gesellschaften umgewandet worden.
Die neuen, modernen Hüttenanlagen forderten Investitionen und die Hochöfen
konzentrierten sich auf einige Hütten während andere stillgelegt wurden. Die Hütte war oft der Mittelpunkt des Dorfes Mittelpunkt mit Schrebergärten,
Wohnungen für die Arbeiter, Kohlenhaus und Erzbunker im nahen Abstand. Hier
lernten die Jungen von den Alten mit Lebenserfahrung, wie die Hochöfen betrieben
und die Schlacke verarbeitet wird. Jeder Abstich war ein Schauspiel, wenn das
Eisen heraus rann, weiß glühend, heiß und unter einem knisternden Heulen. In den
dunklen Winternächten schienen Flammen aus der Hochofengicht und lockten
frierende Wanderer, um sich zu wärmen. Die Herstellung von Roheisen im 18. Jahrhundert erfolgte mit Holzkohle und Erz,
dass im Bergwerk grob gebrochen und geröstet wurde, um es vom Wasser und
Schwefel zu befreien. Ab 1850 wurden Röstöfen eingesetzt, die vom Gichtgas des
Hochofens betrieben wurden. Diese wurden von oben mit Erz gefüllt, das unten
geröstet herauskam und danach von wasserradgetriebenen Mühlen in kleine Stücke
gemahlen wurde. Dann wurde die kleinen Erzstücke in kleinen Wagen „Erzhunde“ zur
Gicht des Hochofens gezogen. Dorthin wurde auch die Holzkohle hochgezogen, die
von einem Kohlenmeiler im Wald zur Verwahrung im Kohlenhaus neben der Hütte
lagerte. Manchmal wurde auch noch Kalk hinzugefügt. Um das Feuer aufrecht zu
erhalten und weil der Kohlenstoffgehalt im Eisen reduziert wurde, benötigte man
auch Luft. In der ersten Zeit wurde die Luft mit Blasebalgen in den Ofen
geblasen. Ab Mitte des 18. Jahrhunderts wurden diese durch Gebläsemaschinen
ersetzt. Zur gleichen Zeit begann man auch die Luft zu vorzuwärmen. Dadurch
konnte man Holzkohle sparen.
Im unteren Teil des Ofens, im so genannten Gestell, wurde das flüssige Eisen
gesammelt, darüber schwamm die Schlacke. Aus der Ausschlagsöffnung floss zuerst
die leichtere Schlacke, die meist in Formen zu Schlackensteinen für die
Bauindustrie verarbeitet wurde. Danach wurde das weiß glühende Eisen
herausgeschlagen. Das rann in einer Abstichrinne in Roheisenformen hinunter, die
zu viereckigen Stücken erstarrten. Das Roheisen wurde anschließend in einem
Holzkohleherd gefrischt und mit einem Hammer zu Stabstahl geschmiedet. Das Roheisen konnte zum Gießen von Kanonen verwendet werden, doch gewöhnlich
wurde es nach dem Frischen in einer Hammerschmiede zu Stabstahl verarbeitet. In
den Schmieden wurde der Stabstahl auch oft veredelt und zu Fertigprodukten wie
Nägel, Hufeisen und Werkzeugen verarbeitet. Der Stabstahl wurde auf dem
internationalen Markt verkauft und waren bis Ende des 18. Jahrhunderts die
größten Exporteinnahmen von Schweden. Die Produktion von Eisen war jedoch
geregelt. Teils, um zu verhindert, dass die Preise zu stark fallen und teils um
den Waldnachwuchs nicht zu gefährden. Die Bergwerke, Hütten und Hämmer
schluckten eine Menge Holzkohle. Um den Wald richtig zu bewirtschaften, war es
notwendig die Eisenverarbeitung zu rationieren.
|